Kicking up dust in Long Beach
What is BajaSAE?
“Baja” is an annual engineering competition organized by the Society of Automotive Engineers in which teams are tasked with designing a production oriented single seat offroad vehicle capable of traversing a multitude of terrain types and obstacles. Vehicles are to be built around a strict set of rules and regulations, while being loose enough to allot individual team freedom in terms of individual subsystem design. Competitions vary in track design and location while retaining similar event types, meaning vehicles must be flexible to what they are capable of doing. In addition to this, teams are encouraged to follow practices and engineering cycles already found in the industry in order to further simulate a real product life cycle.
My Baja Experience
Despite only being a college sophomore, my time in SAE has made me a better engineer by teaching concepts and ideas that are not found in class, often times through hard lessons. As a second year mechanical engineering student, I currently hold the title of rear suspension lead. As lead, I am partly in charge of overseeing the development and fabrication of all things related to the suspension control systems in the rear of the vehicle. On the team, I currently manage a subsystem of over 20 people all working together on integrating new components for the current and next iteration of the Baja car. In addition to my responsibilities as a lead, I have a habit of becoming involved with other areas of the club. Notable examples include the fabrication of our chromoly spaceframe, emergency fixes for our flawed steering geometry and engine mount, and even the tuning of our constant variable transmission unit (in which we collaborated directly with the manufacturer in addition to industry professionals). It is here where I have been best able to grow as both a person, and as an engineer by developing hard and soft skills. Some skills include manufacturing via machine operation (lathe, mill, some CNC, etc.) real world CAD modeling, fabrication (and all that comes with it), electrical knowledge, communication skills (150+ members on our team), and even driving skills (as of recent).
Despite my short time on this team, I have experienced most of what goes into a real world product development cycle and all the necessary troubleshooting processes that normally arise post production.
2024/25 Plans
As of now, plans for the upcoming iteration include correcting our suspension geometry and fixing several underlying issues in our knuckle design. We aim to gain a defined consistent camber curve (the car as of now gains camber as the chassis enters roll),and aim to integrate seals into our knuckle, along with redesigning components that did not have hardware (and the physical space it occupies) in mind initially. In addition to this, we aim to simplify the disassembly process and decrease the time associated with it through correcting several mounting tabs that were not properly positioned before welding. All of these changes will present quantifiable results which will be listed here as soon as they are available.
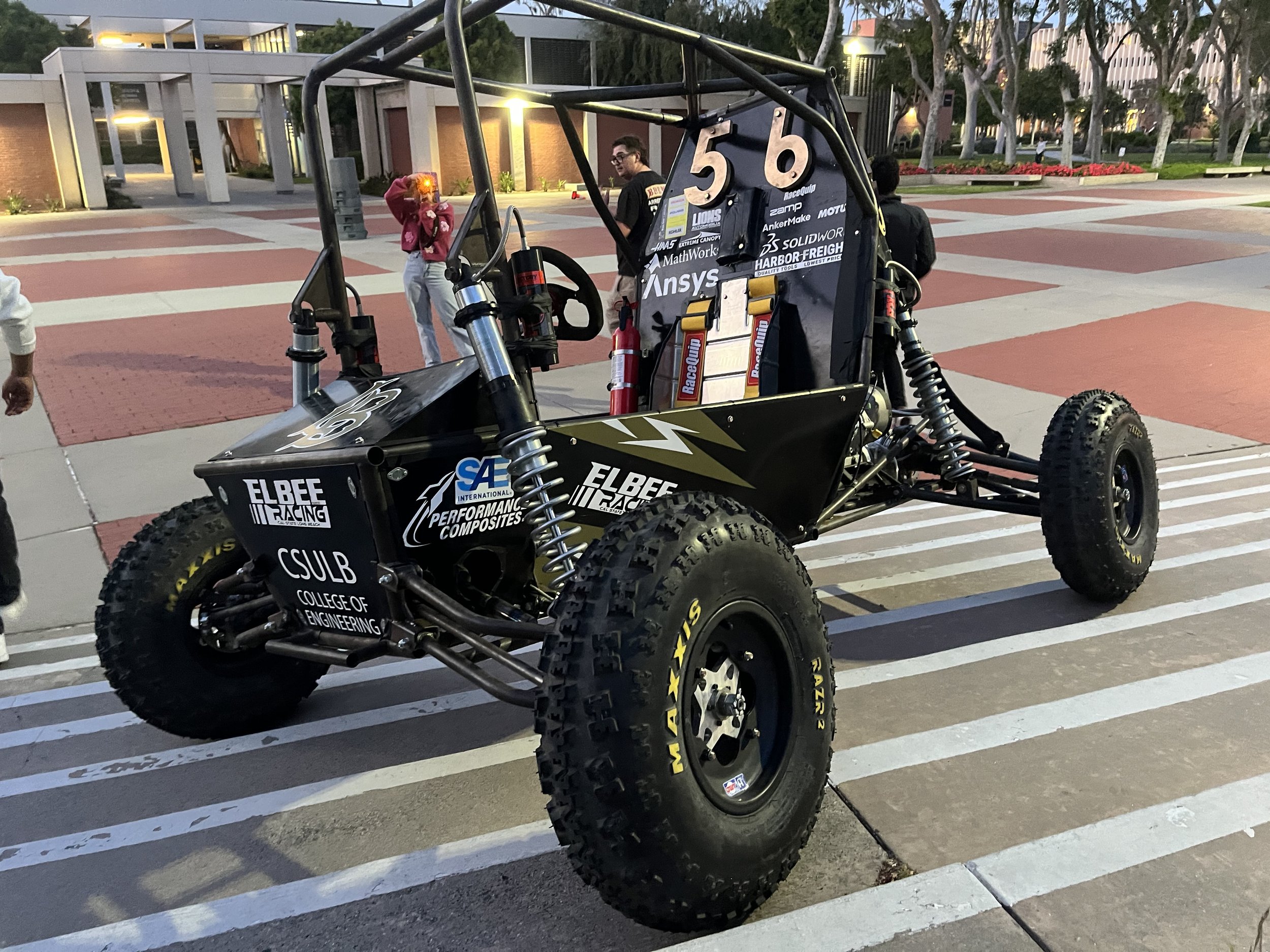
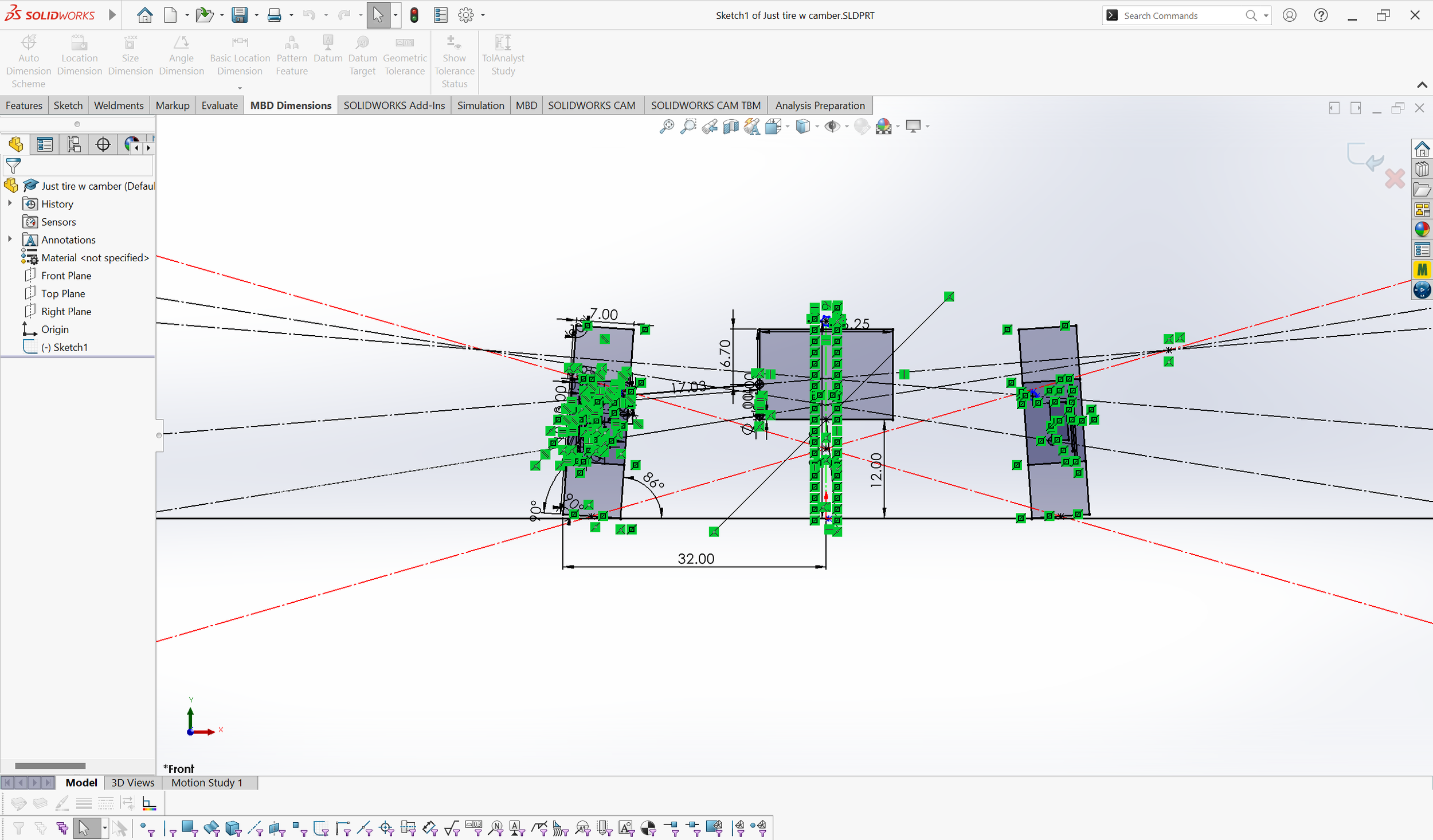
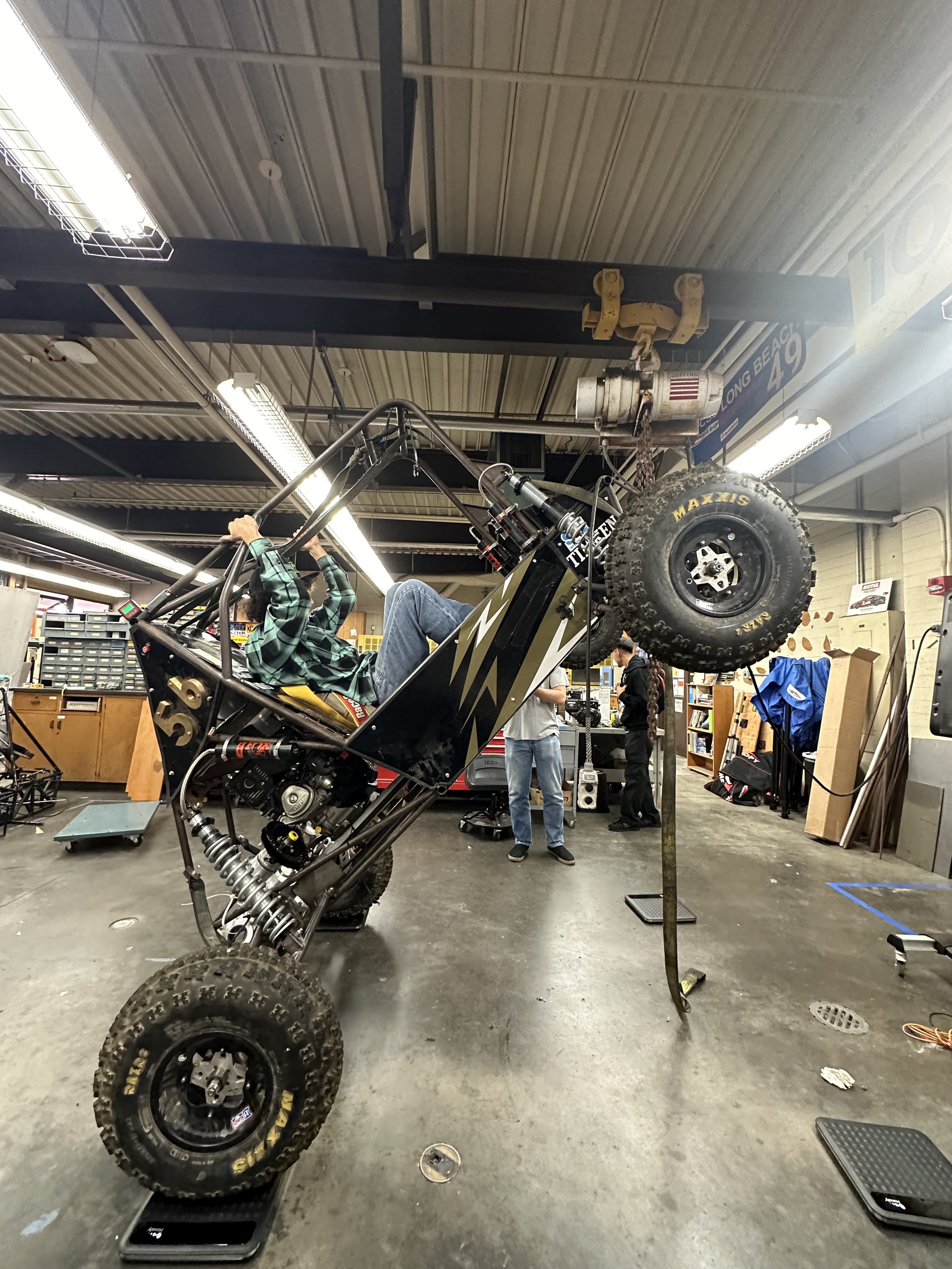
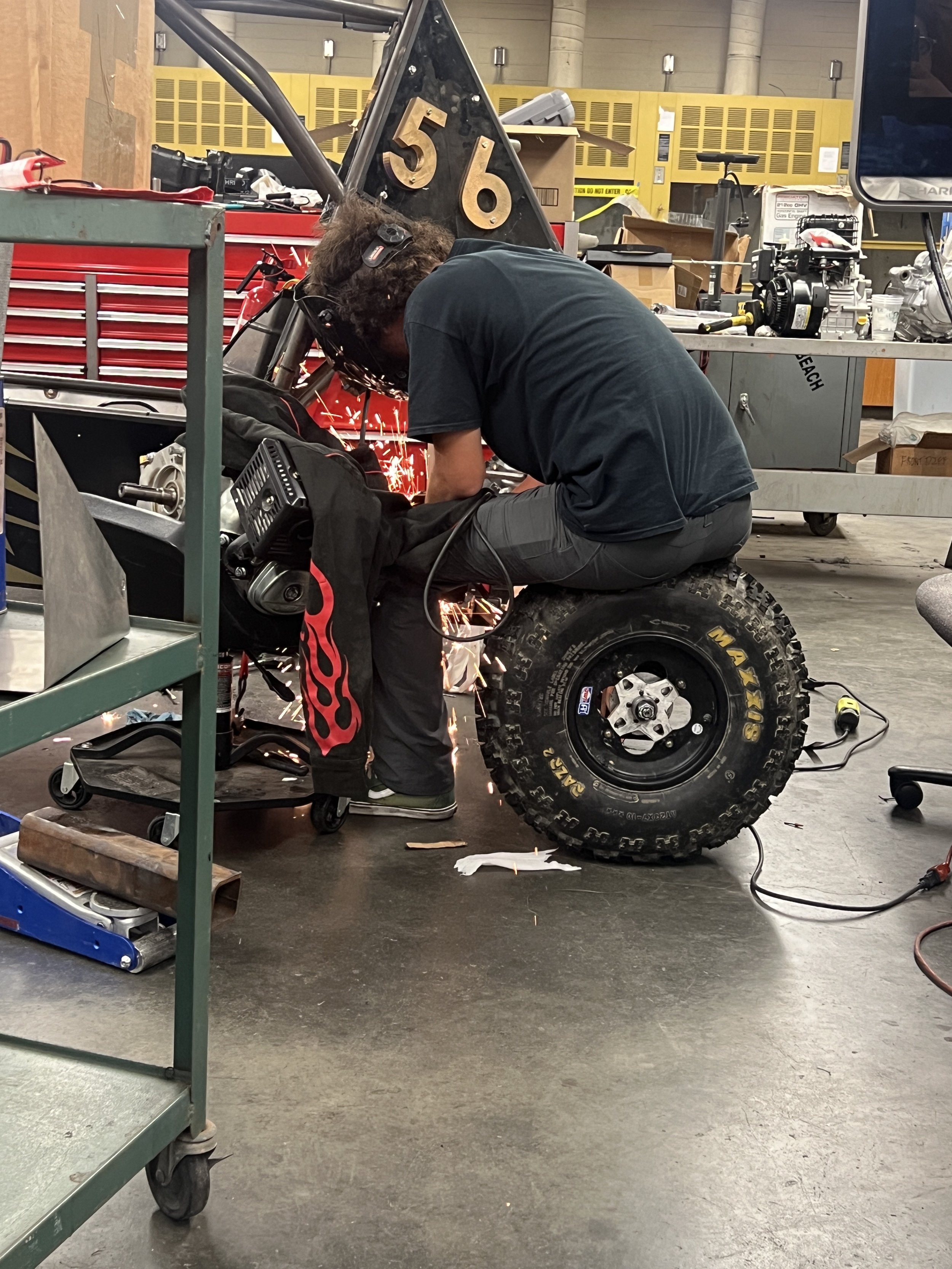
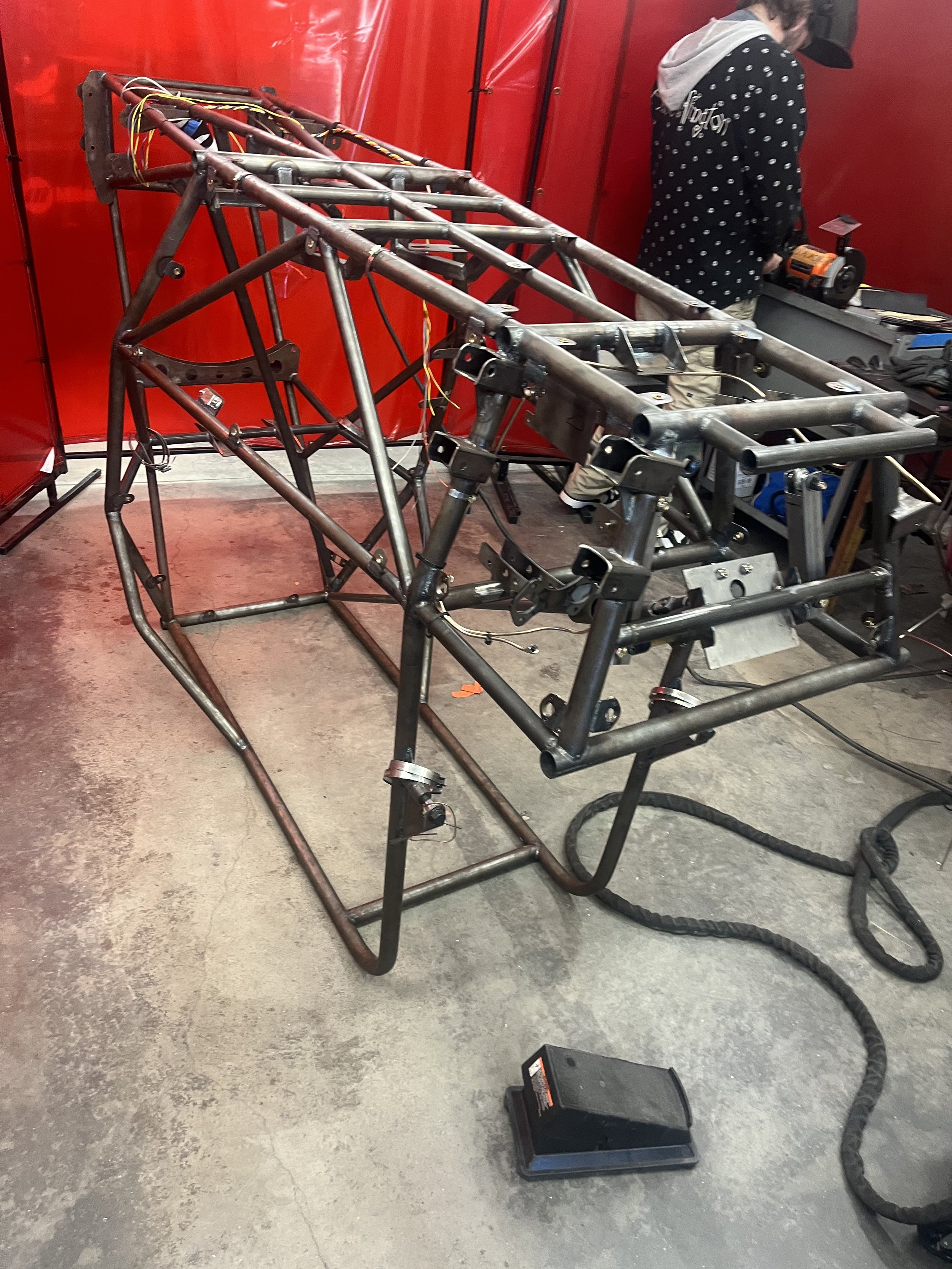
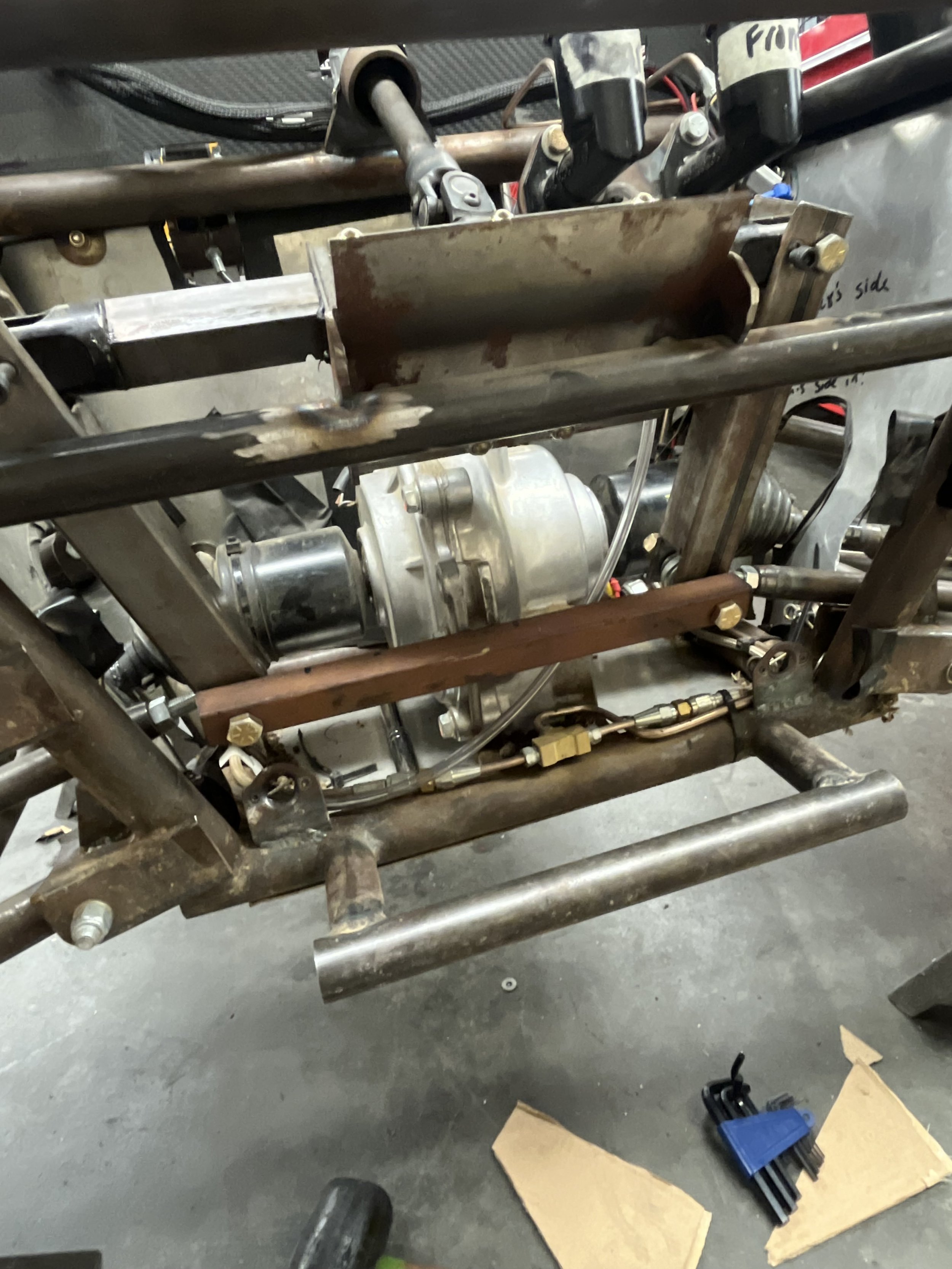
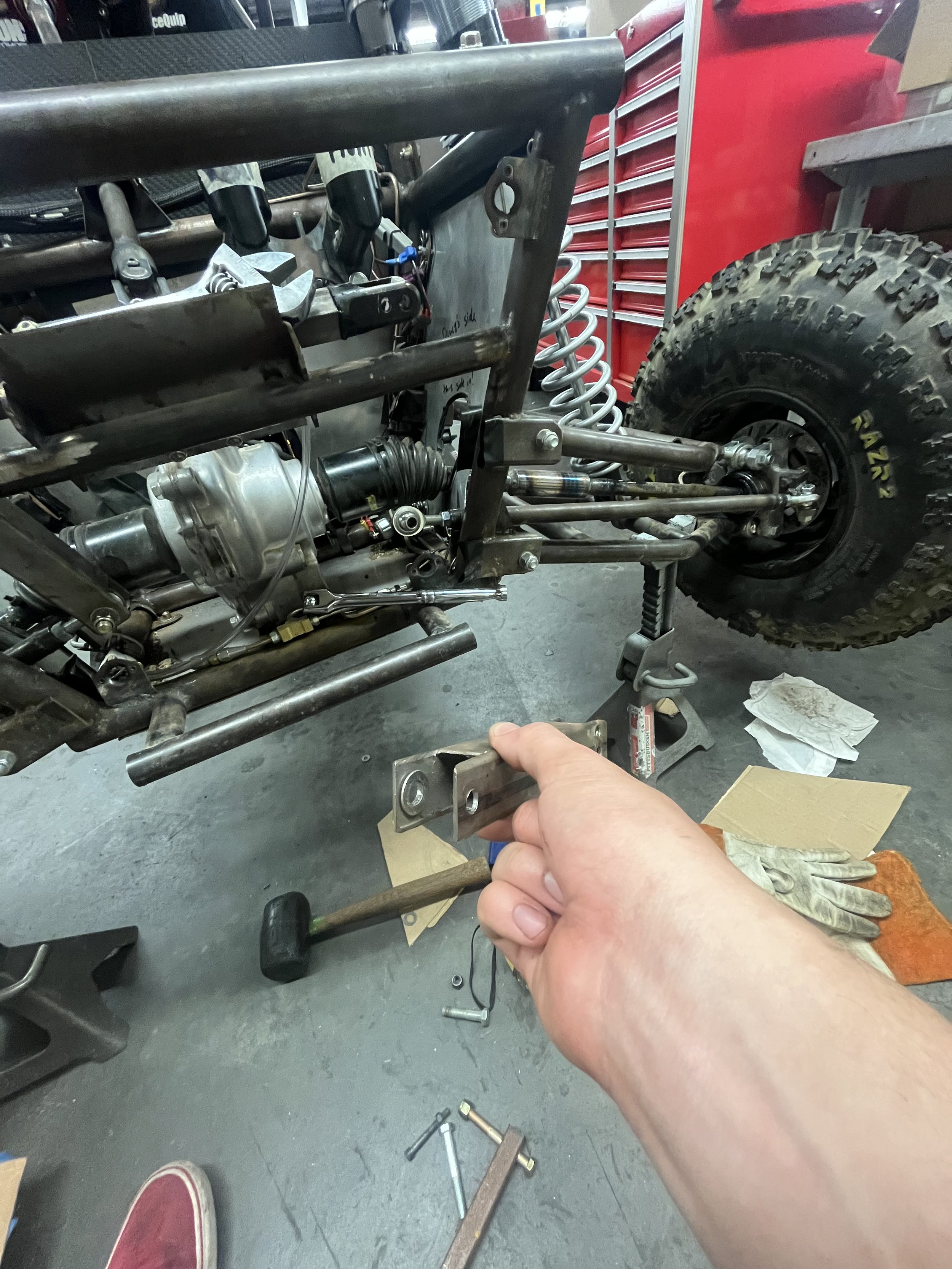
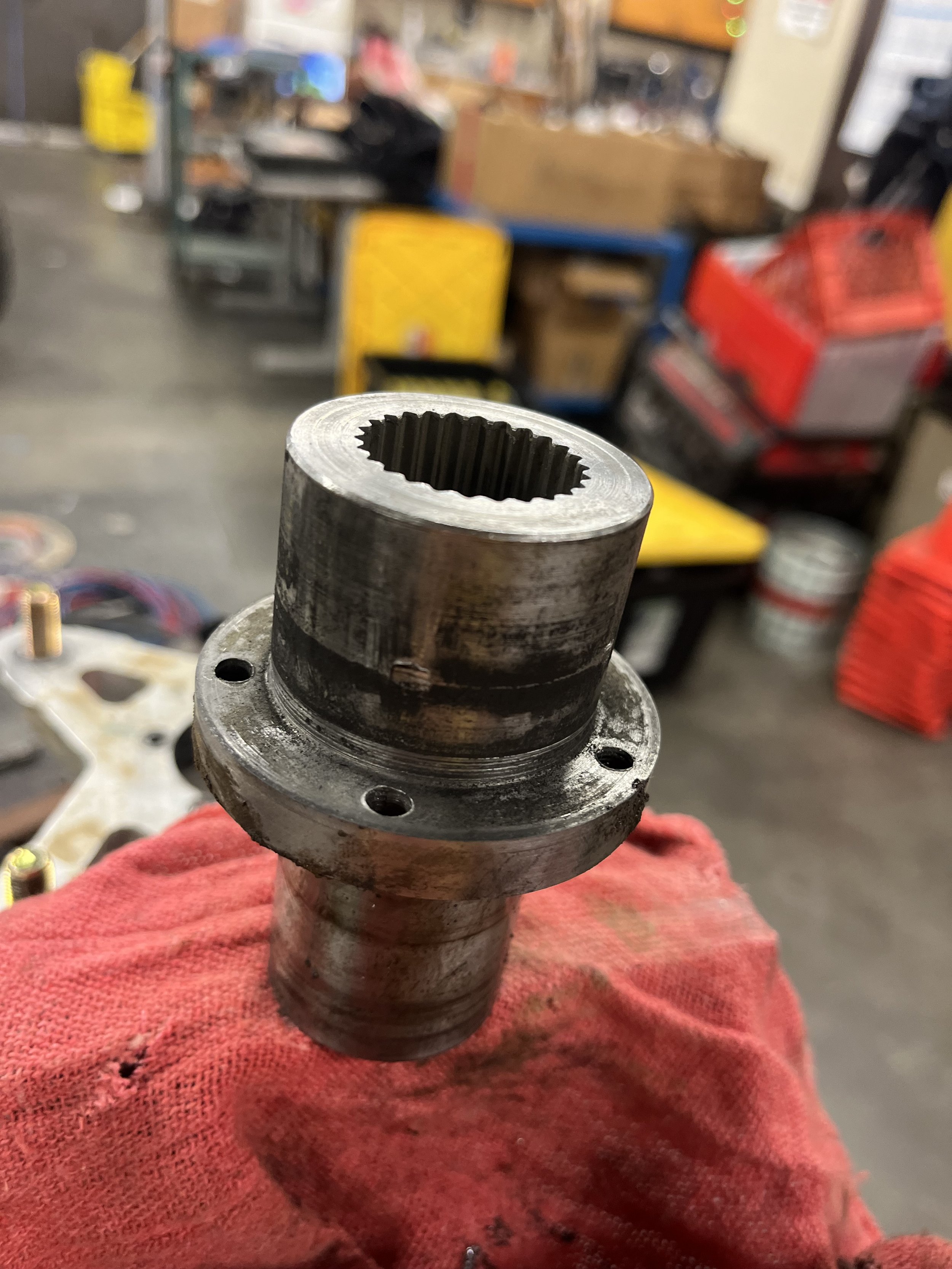
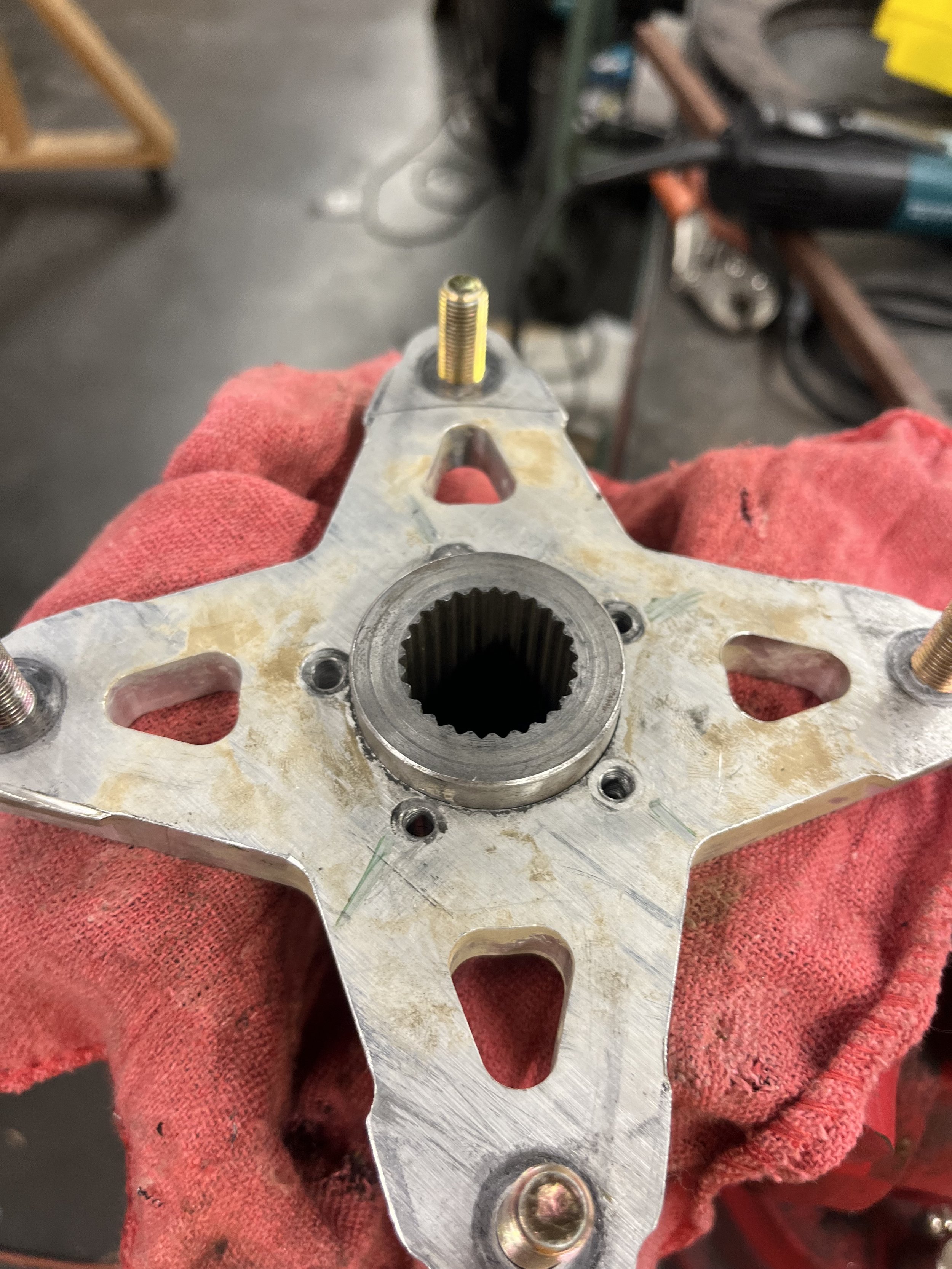
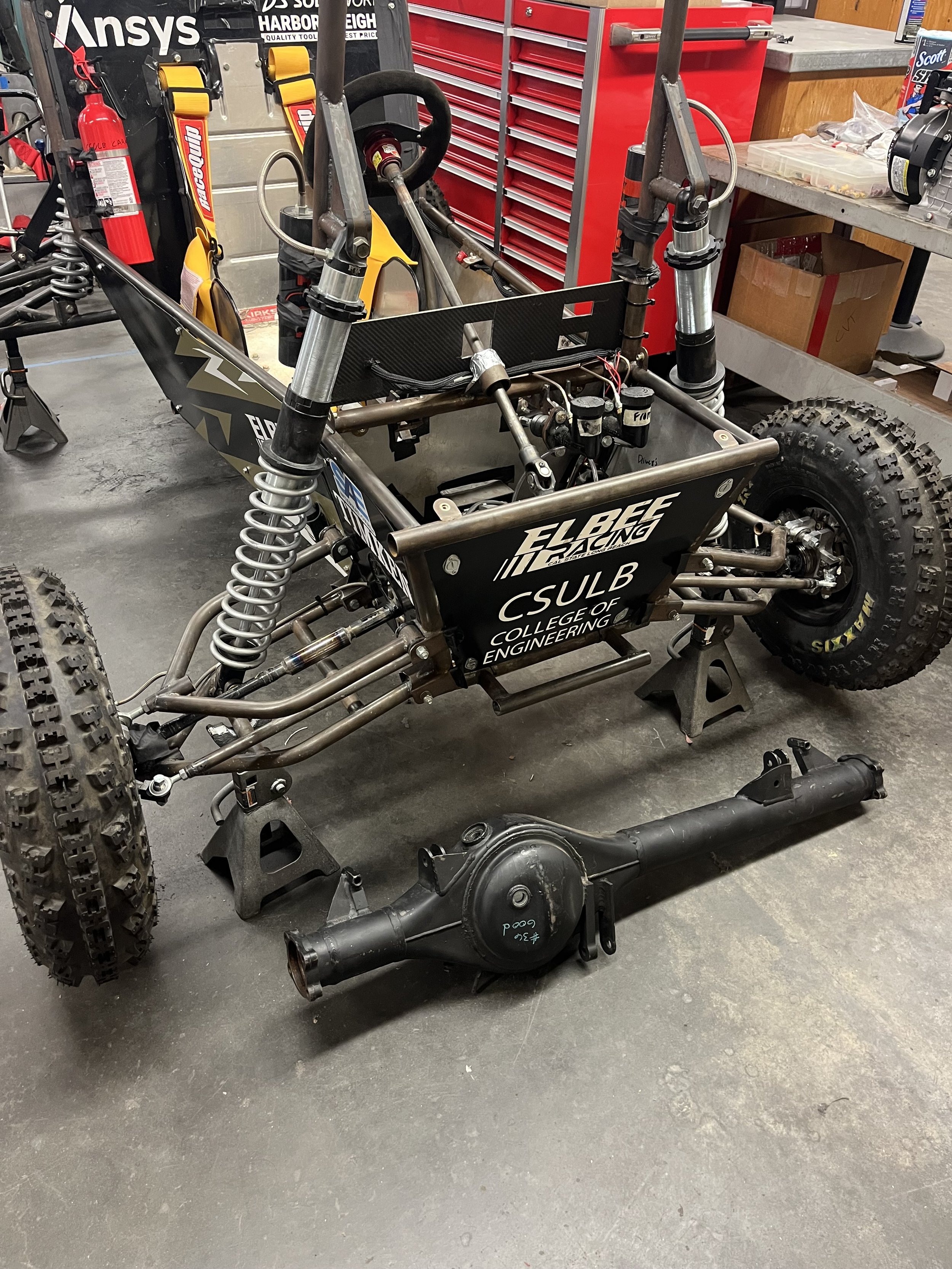

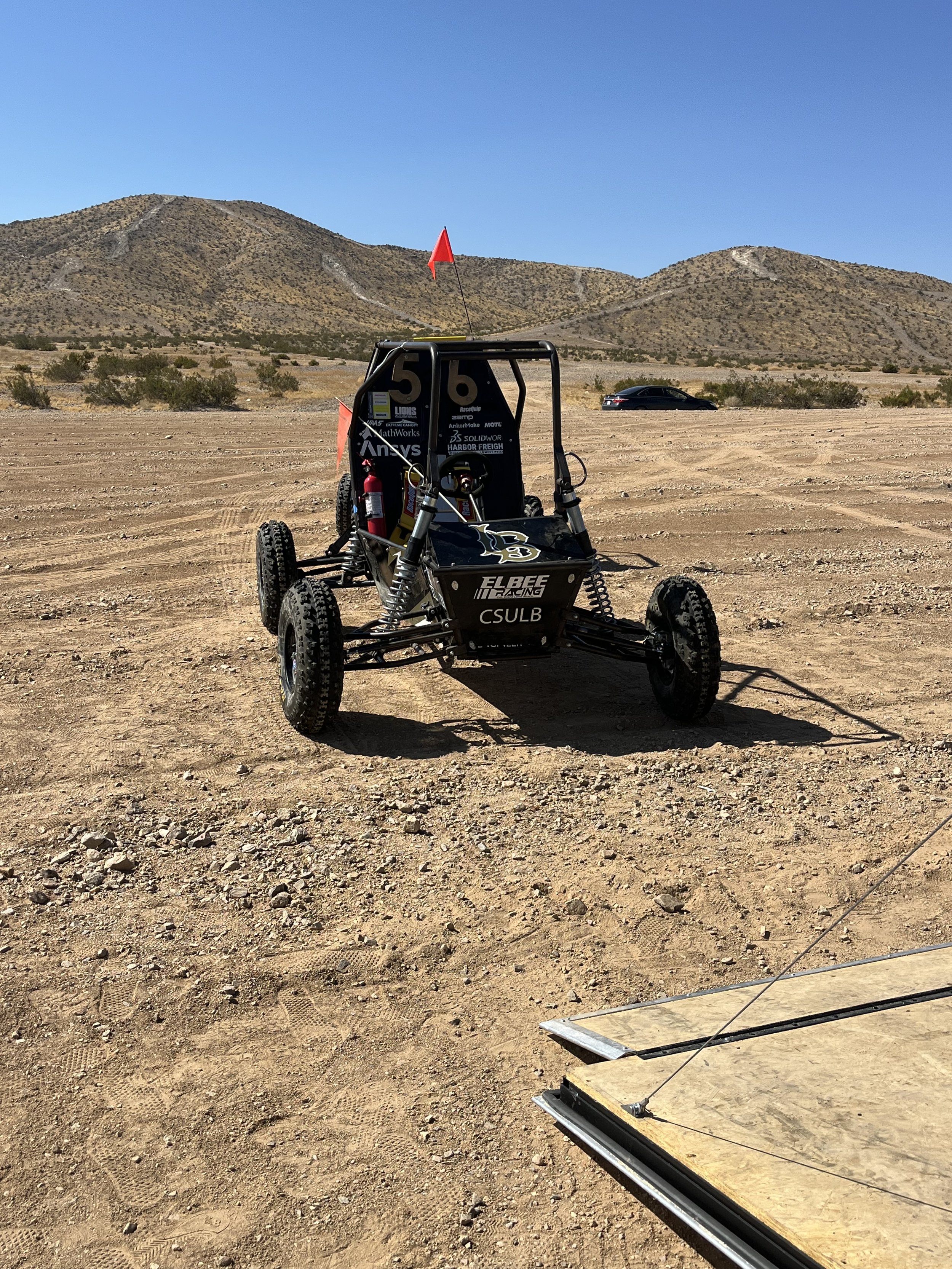
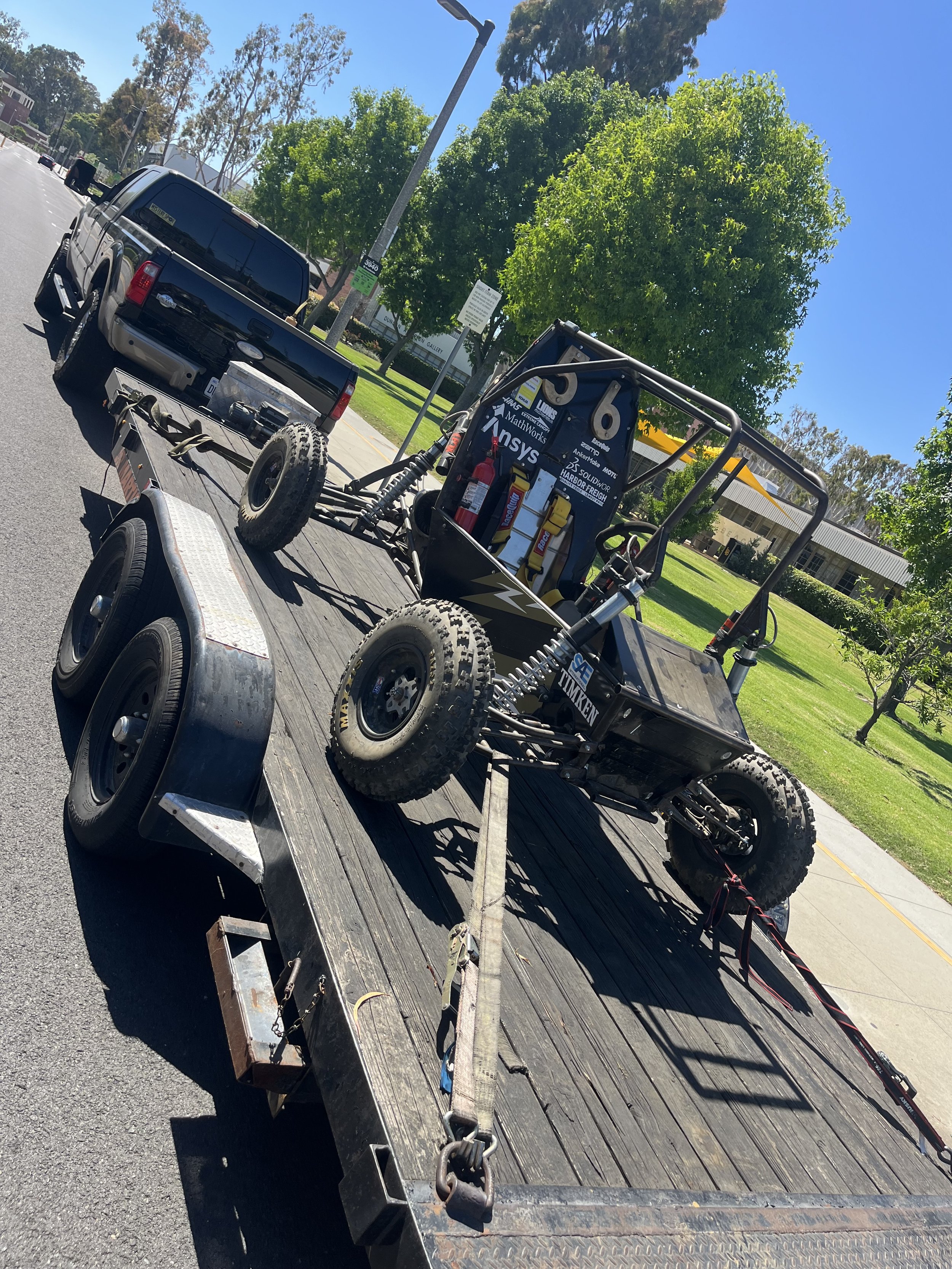
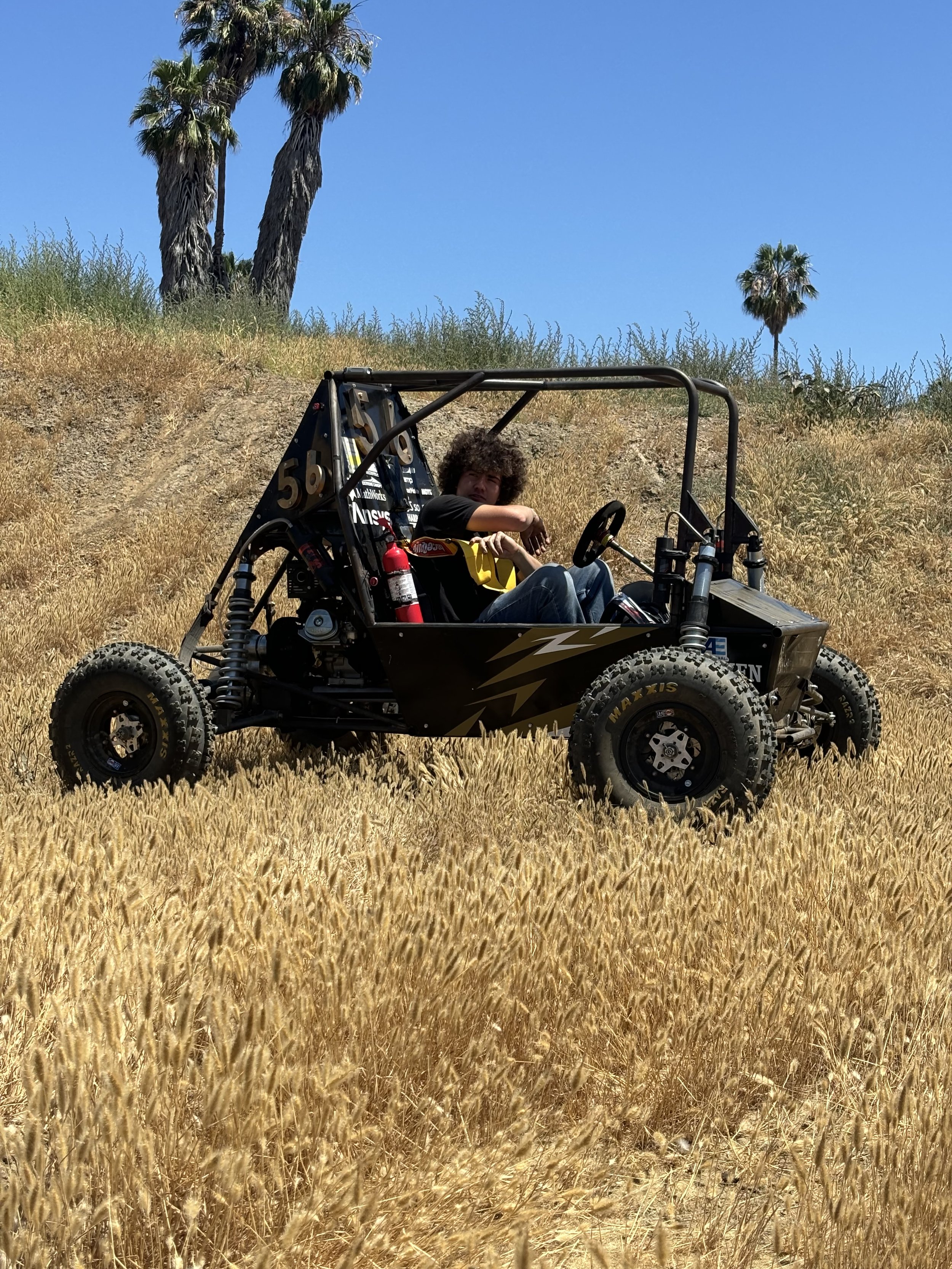
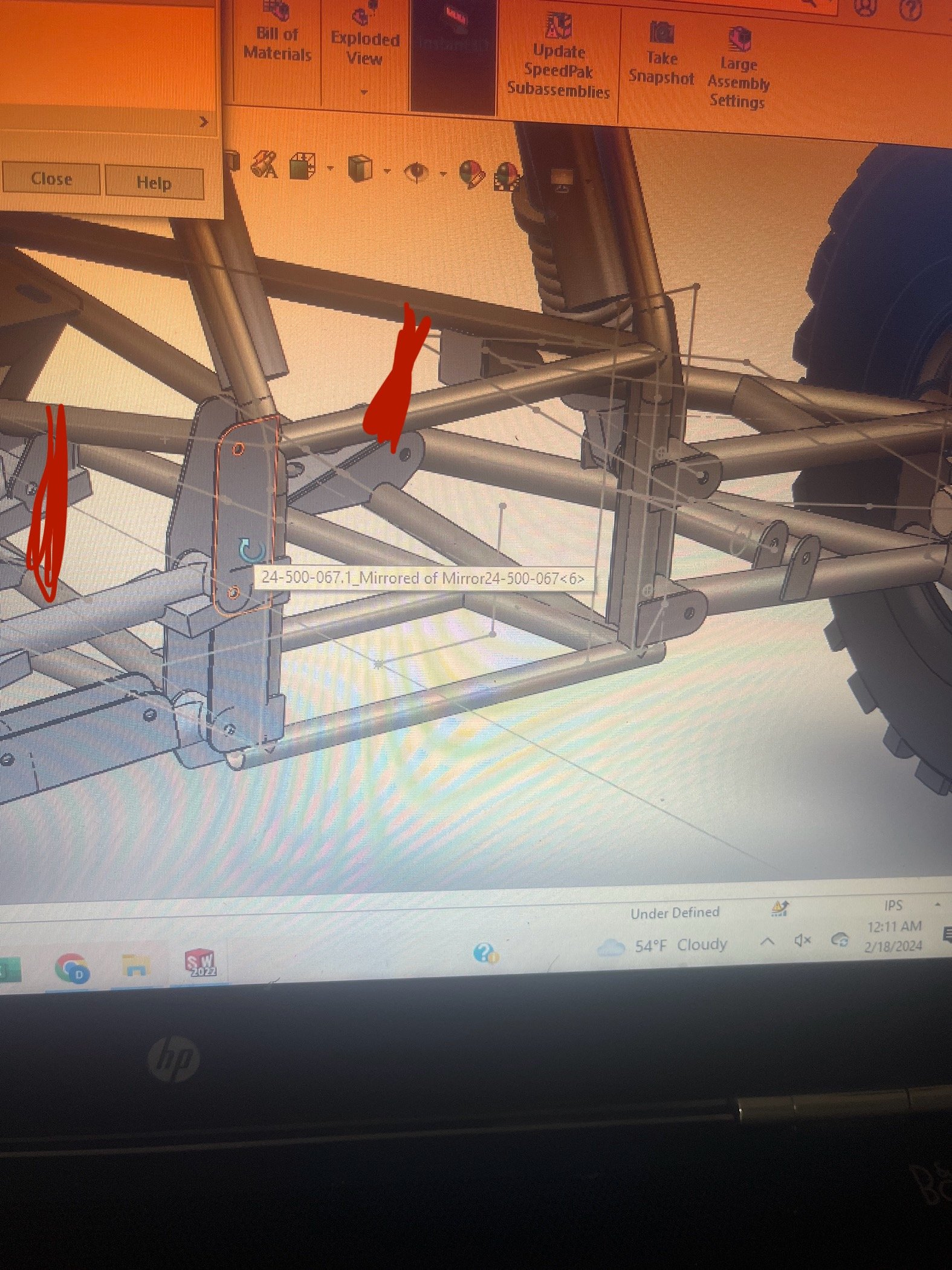
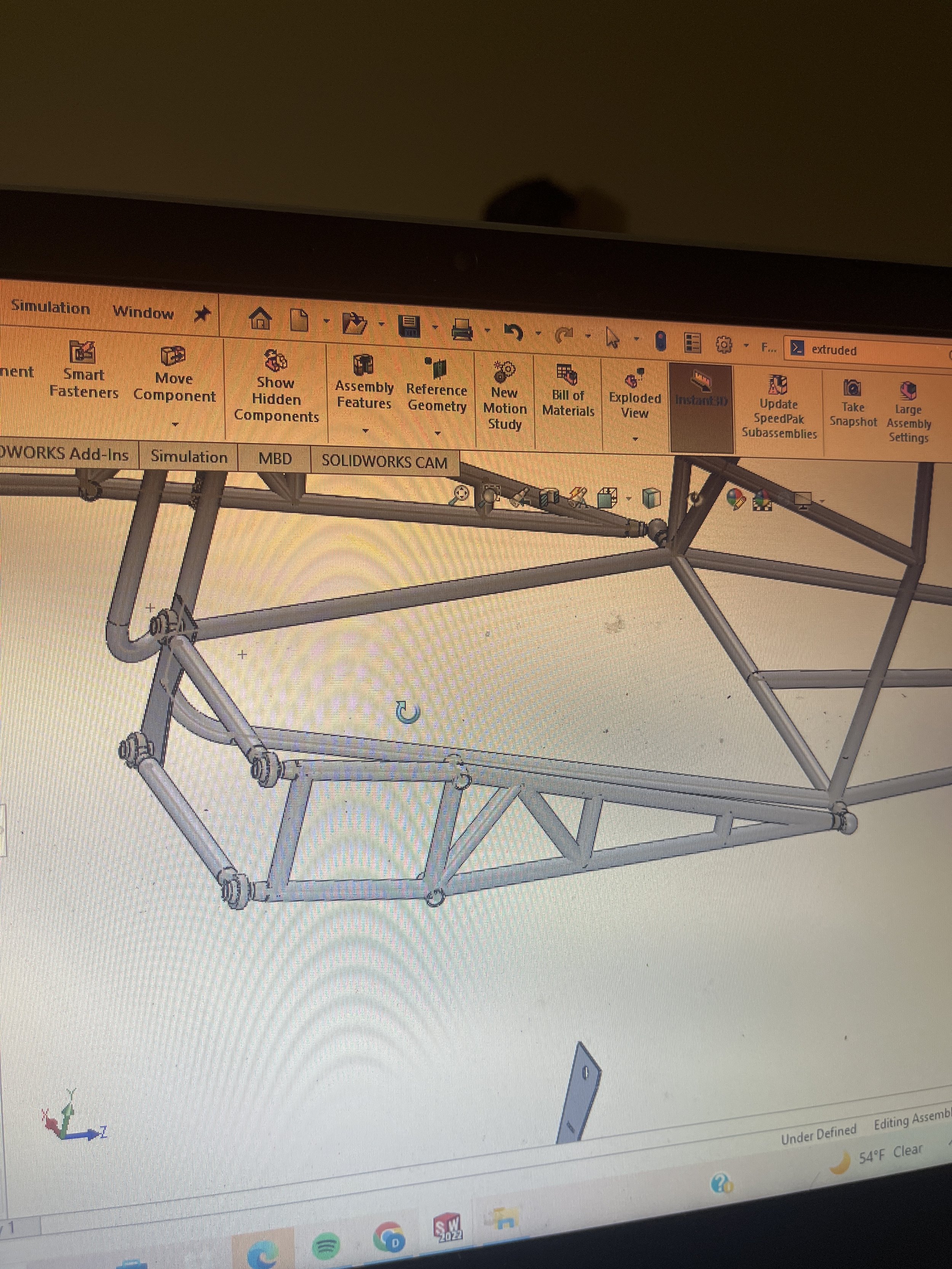
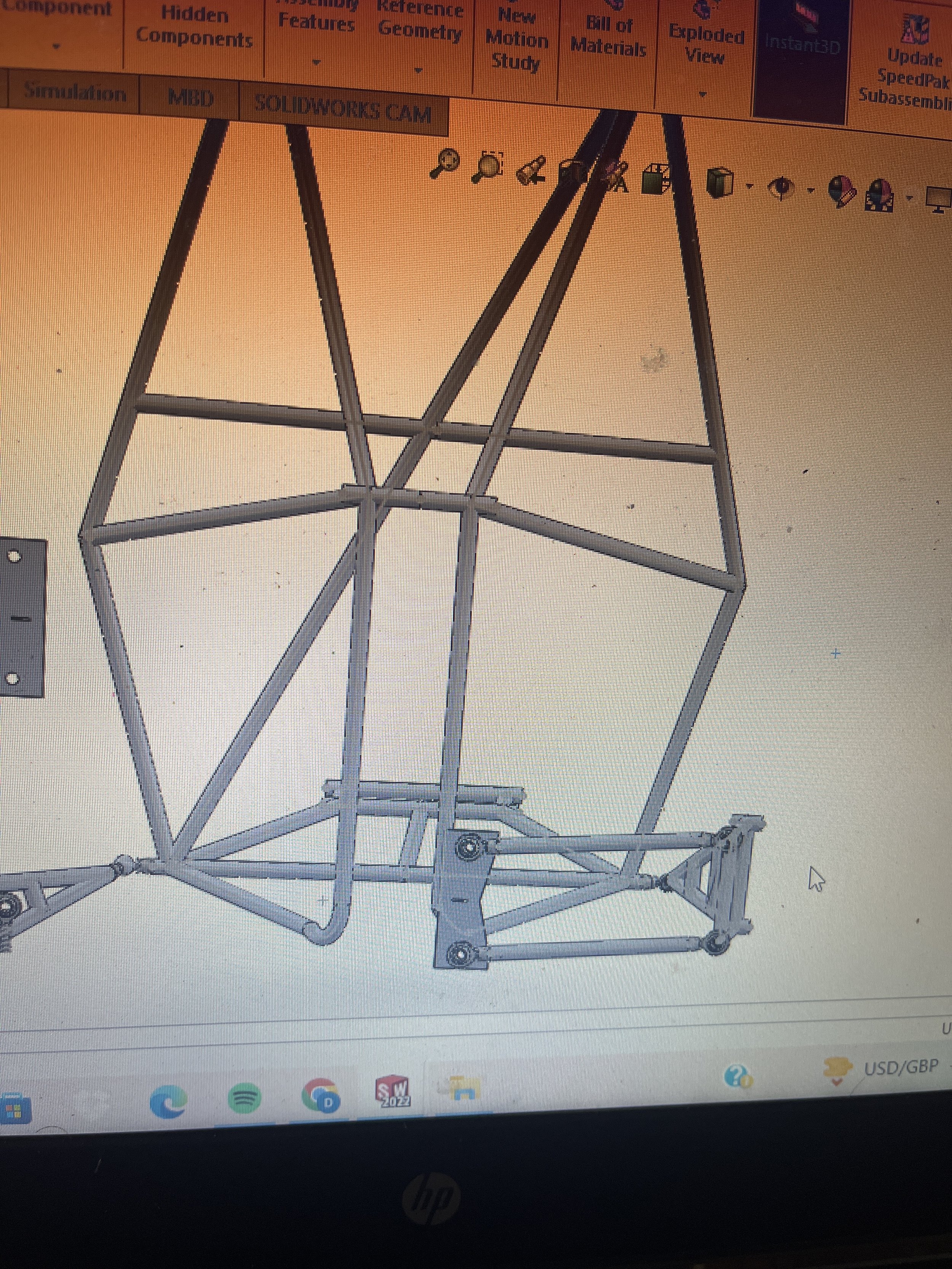
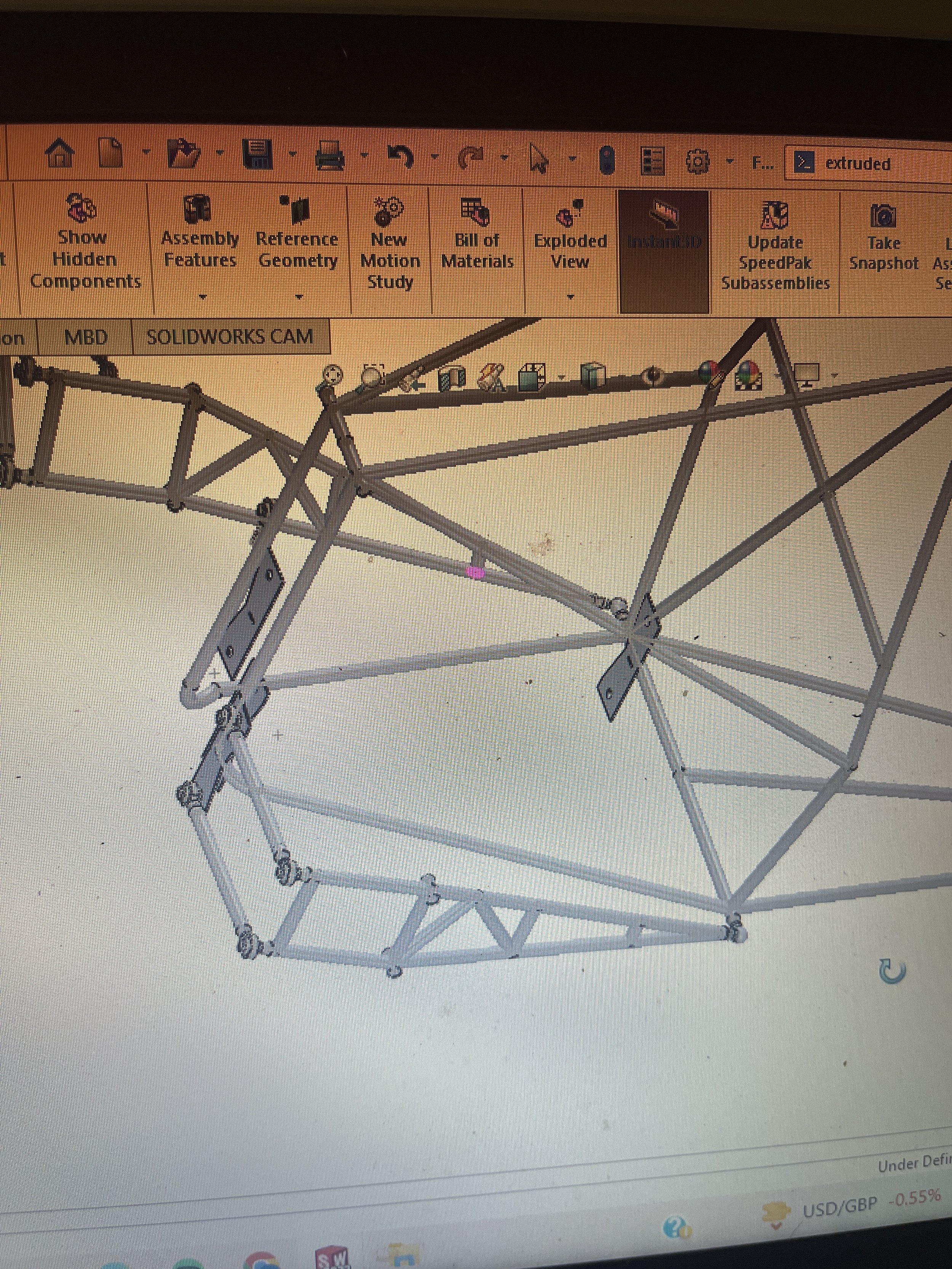

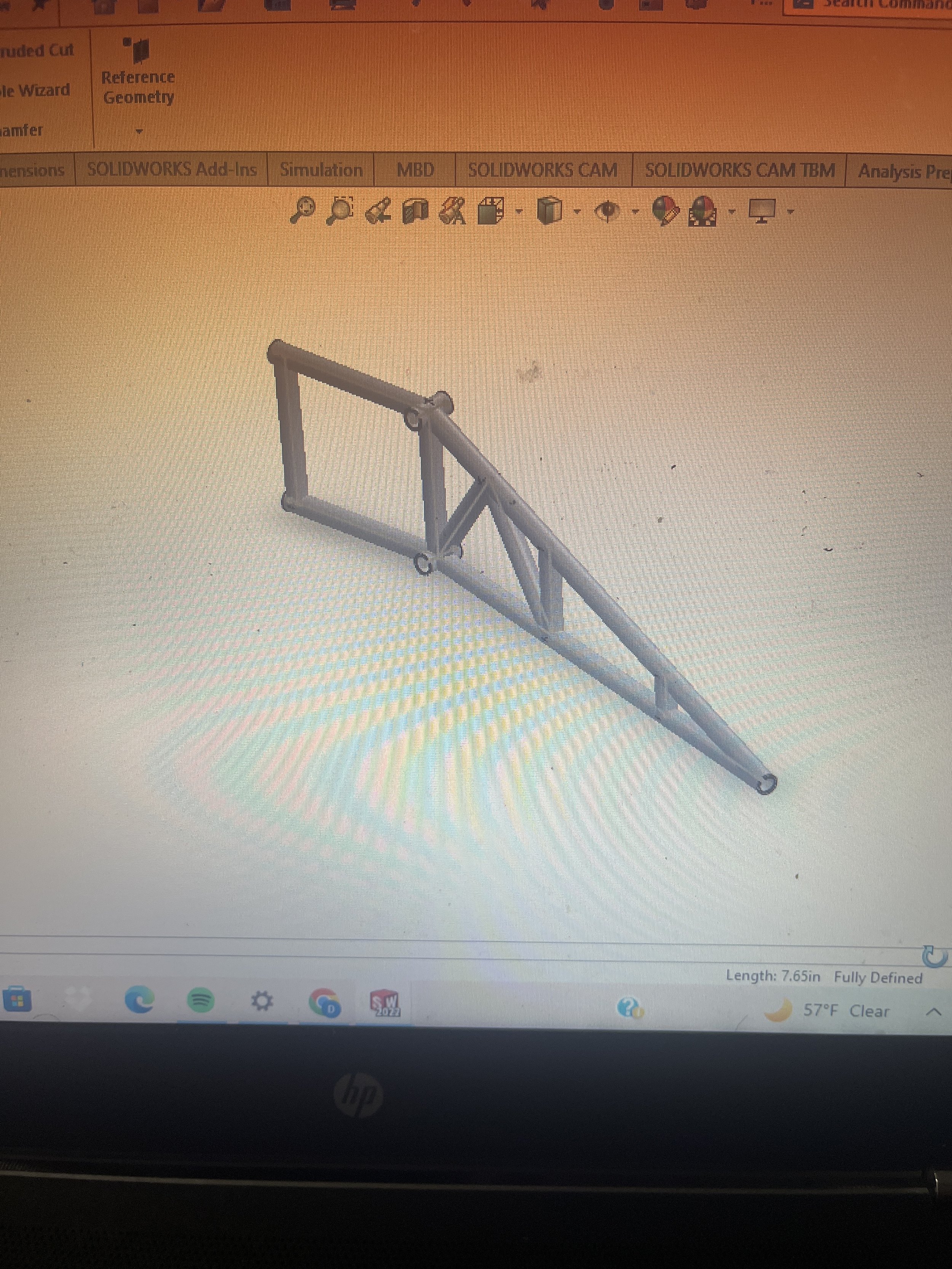
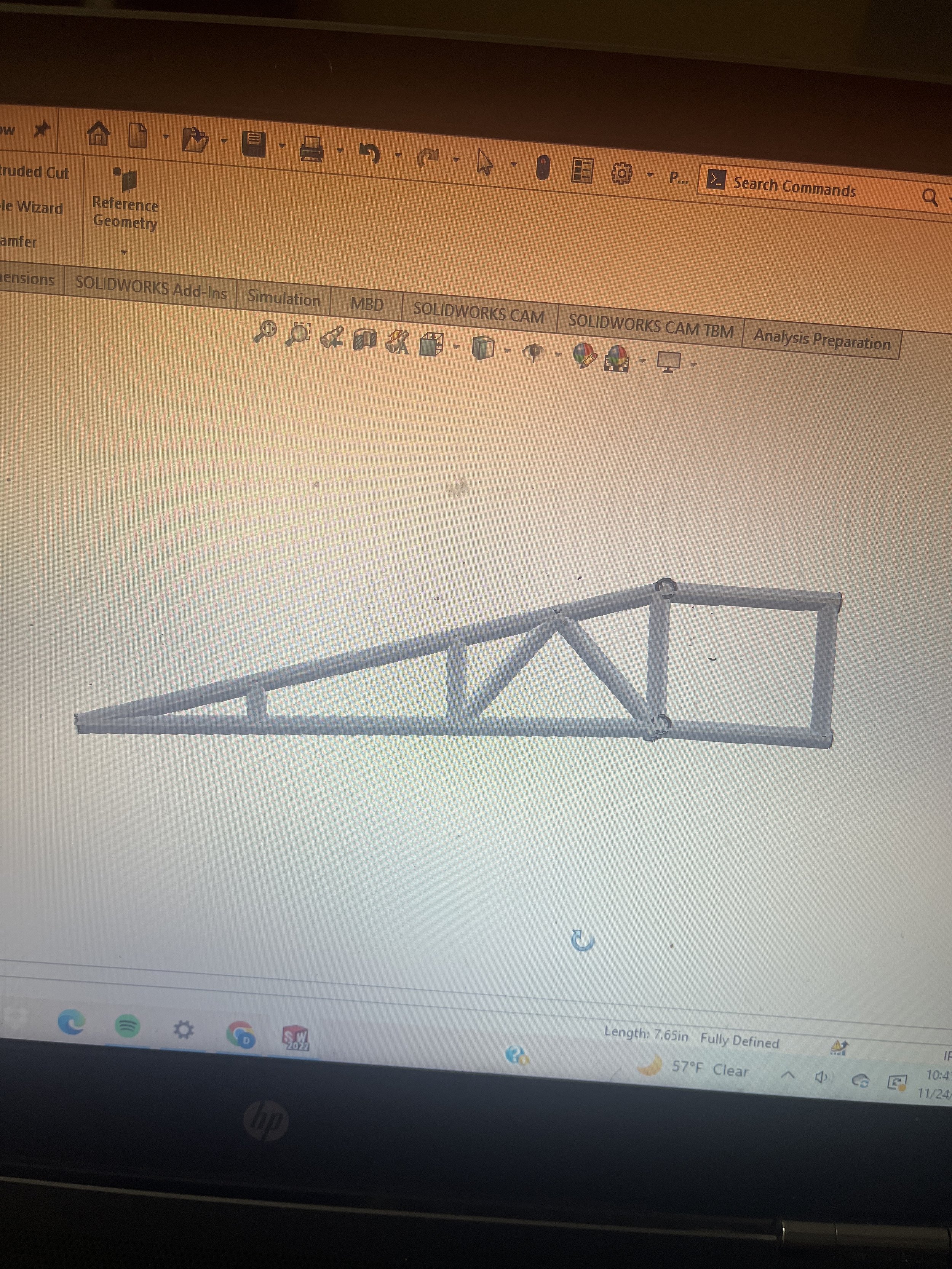

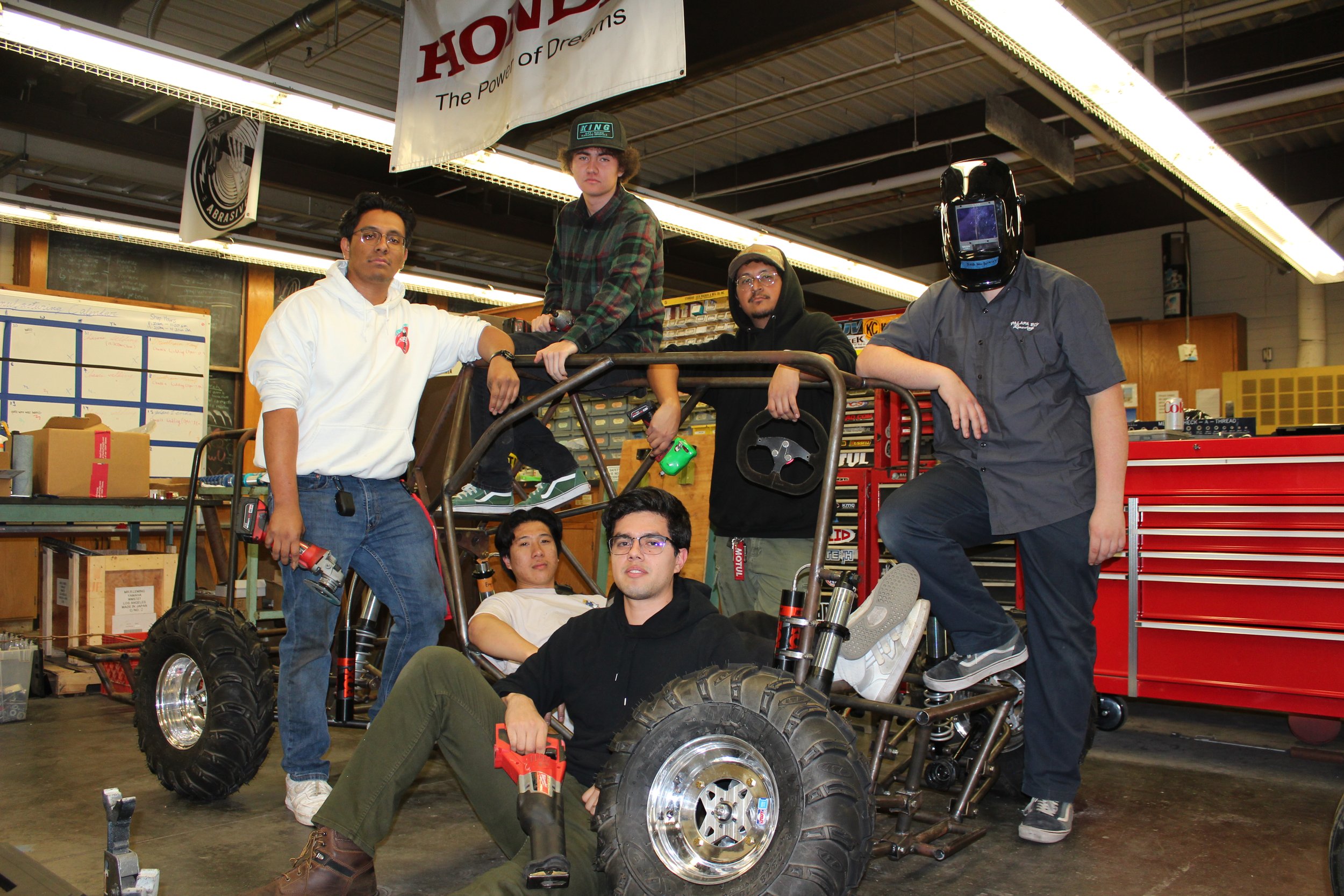